One of the most utilized applications for investment casting is for the design and manufacture of a wide range of components to be utilized in petrochemical engineering. Each of these investment castings serves a crucial role in ensuring the functionality and safety of petrochemical processes around the world.Â
These investment-cast components must be strong and stay strong through extremely harsh conditions and extreme temperatures. They must be able to meet the goal of being some of the most corrosion-resistant components used throughout the industry and maintain structural integrity over extended periods.Â
The proper selection and application of metal casting parts are crucial to prevent system failures, leaks, and potential hazards, thereby safeguarding the environment, personnel, and assets involved in petrochemical operations. In the petrochemical sector, a single failure can lead to catastrophic consequences. That’s why Niagara Investment Castings produces precision cast parts with high levels of accuracy, strength, and proven performance over a long period of installation in some of the most crucial pieces of industrial equipment and machinery.
The Process of Manufacturing Investment Cast Petrochemical Components
Niagara Investment Castings is proud of our long history in working with manufacturers of petrochemical processing equipment throughout North America. More often than not, these clients require unique designs, large castings, and super alloys that often include their own proprietary high temperature, severe service super-alloys.
Investment cast petrochemical components start just as any other investment casting would, and that is as wax injections using highly detailed aluminum injection dies to produce incredibly smooth surfaces on the patterns, and as much detail as needed. For lower volumes or prototype samples, we can 3D print the pattern in plastic and use that in substitution of the usual wax pattern.
The patterns are coated with a ceramic slurry and allowed to dry and built up layer by layer until a seamless self supporting mold is formed. The pattern is melted out, and the mold is filled with a molten alloy suitable for the final application of the petrochemical component.
We work with our clients and their metallurgical teams to produce castings in highly specialized alloys that perform above and beyond commercially available metals. We manufacture investment castings up to 200 pounds in weight, easily meeting the requirements of our clients for producing large Elbows, Bifurcates, and more. We provide our clients with the high level of testing these critical application castings require, including traceable chemical and mechanical testing, radiography and liquid penetrant testing, and much more to verify the integrity of our castings.
What Petrochemical Components Can Be Cast
The investment casting process offers an unlimited number of possibilities when designing components for petrochemical applications. There is a wide range of components used in petrochemical engineering. For example, valves control the flow of fluids and regulate the movement of gases, liquids and hazardous substances. Pumps facilitate fluid transport throughout the petrochemical infrastructure. Fittings and connectors enable seamless integration of various components. Structural components lend strength and heat resistance to components that need to stay strong through extreme high temperatures.
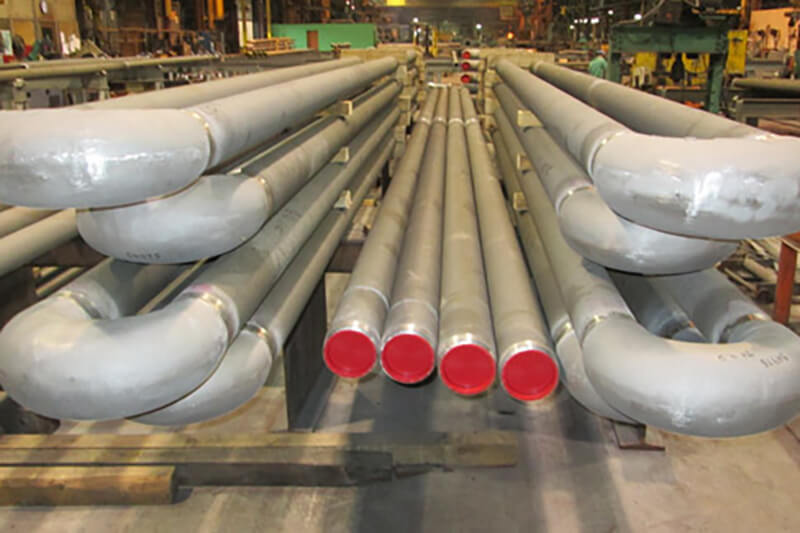
Examples of Petrochemical Products Produced:
- Lifting Lugs
- Elbows and Tees
- Bifurcates
- Catalyst Plates and cones
- Reducers
- Furnace tubes and components
- Hangers and mounts
- Guides
- Pins
- Recuperator components
- Tuyeres
- Riders
- Grids
Large Component Investment Casting
There are often large castings utilized for pump bodies, impellers, and seals, as well as valve bodies and the various types of discs used in the valve. While typical investment castings are generally smaller to take advantage of the precision of the IC process and superior surface finish, many larger castings can also benefit from these characteristics.
To produce larger than normal investment castings requires the foundry to anticipate the need for larger wax presses, larger and higher capacity ceramic shell tanks, robotics for the handling of much larger molds, and higher melting and pouring capacity.
While this is not common among investment casting plants in North America, we are proud that Niagara Investment Castings anticipated the need for large castings for the petrochemical industry many years ago and can offer investment castings up to 200 pounds in weight to satisfy this requirement.
Advantages of Investment Casting for The Petrochemical Industry
There are many reasons why manufacturers worldwide choose investment castings to produce the many types of components used in the petrochemical industry. Some of those reasons are as follows :
Material Selection of Investment Cast Petrochemical Components
- Material selection is based on factors like temperature, chemical exposure, and mechanical requirements. Choosing the right material ensures optimal performance and durability of cast parts, and our expertise will help our clients with these decisions.
- High temps and corrosive environments demand specific materials for metal cast parts. Many companies will design their own proprietary alloys for these reasons, and NIC is proud to work closely with our clients to pour their own specialty alloys for their castings.
- Petrochemical industry components must be able to withstand extreme heat and resist corrosion in challenging environments. Various materials offered by NIC, such as stainless steel and nickel alloys, are commonly utilized. These materials offer excellent heat resistance and corrosion protection for cast parts.
Design Freedom
Petrochemical engineering involves a wide range of equipment and systems, each of which has components that can be investment cast. Common metal cast components in this field include valves, pumps, flanges, fittings, connectors and various structural elements.
These parts are designed and manufactured to take advantage of the design freedoms that investment casting offers. Complex geometries needed for impellers are formed easily without the need for finish machining of the volute pattern in many cases. Complex passageways throughout the pump, valves, meters, gauges and pipelines, are achieved by the various coring techniques available with investment castings, and all with the smoothest surfaces available by any forming process outside of machining.
These investment cast components are more than cable to withstand the harsh conditions of petrochemical processes.
Certifications of Investment Cast Petrochemical Components
To meet the industry’s most demanding standards, our castings undergo extensive non-destructive testing (NDT) as well as chemical and mechanical testing and certifications, including:
- X-ray inspection – Detects internal defects for maximum reliability.
- Magnetic particle testing – Identifies surface and subsurface irregularities.
- Dye penetrant inspection – Ensures structural integrity at the surface of the casting.
- Pressure testing to ensure leak-proof performance.
- Chemical analyses certification with traceability to heat numbers
- Mechanical testing such as tensile strength, charpy impact testing, and high temperature creep testing
Choose Niagara Investment Castings For Your Petrochemical Casting Applications
With decades of experience manufacturing high-quality investment castings for the petrochemical industry, we are proud of our history of utilizing this unique manufacturing process to satisfy our clients’ requirements.
Contact us to start the discussion today.