Within most industries, the word machine can take on two separate meanings. The first definition would include a general description of the multitude of equipment used to carry out a process via mechanical means rather than by humans.
Machinery allows for greater productivity, ability, efficiency, and power than could ever be possible without these devices that have been designed and manufactured for centuries.
The second meaning of the word machine in industry refers to the process of removing metal from generic shapes using cutting tools to create the final metal components that all machinery is comprised of. This would include CNC machining, manual machining using lathes and milling machines, grinding, honing, and EDM processes.
Niagara Investment Castings manufactures a wide range of cast metal components in over 200 different alloys, which can satisfy the requirements for both definitions of the word “machine”. Many of these castings find their way to our machine shop clients, who in turn process the casting into highly precise components that eventually are installed as crucial components in the many thousands of machines that we have come to depend on to provide us with the standard of living we enjoy today.
With the range of metals we produce and the ability to cast up to 200-pound components, there is virtually nothing we cannot produce, often at a reduced cost and with more detail than other processes can offer.
Investment Casting Parts for Machining
The investment casting process is the perfect complement to the machine shop industry. Starting to produce a metal component using a “near-net shape” investment casting versus starting with a generic “shape”, such as a block or slab of metal allows the manufacturer to have less material to remove during the machining process. In some cases, details that are difficult or impossible to machine can be cast to size, provided the working tolerances permit that.
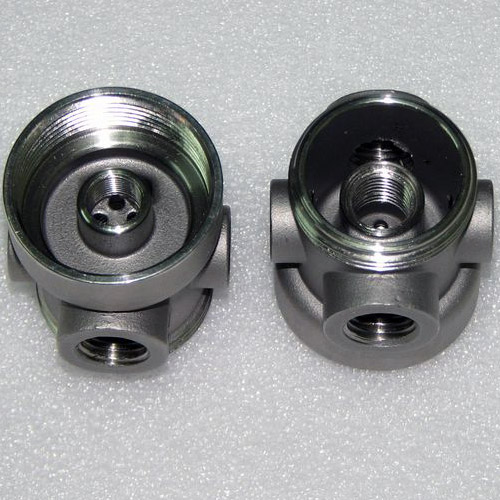
Benefits of Investment Casting for Machine Shops:
Reduced Machining Time and Costs
Investment casting creates near-net-shape parts, minimizing the amount of material that needs to be removed during machining, thus reducing machining time and associated costs.
Complex Geometries and Internal Features
Investment casting excels at producing parts with intricate designs and internal features like passages and cavities, which can be challenging to achieve with traditional machining methods.
Improved Efficiency
By producing parts with near-net shape, investment casting streamlines the manufacturing process, reduces material waste, and minimizes handling and inspection costs.
Tight Tolerances
Investment casting can achieve tight tolerances, ensuring parts fit seamlessly within complex assemblies.
Cost-Effective Solutions
While the initial investment in tooling can be higher, the reduced machining time and costs can make investment casting a cost-effective solution for complex parts.
When You Can’t Rely on Hard Tooling
If your needs are more time-critical, you have a small batch requirement, or you haven’t perfected your design, Niagara Investment Castings can produce investment castings without hard tooling using 3D printing of the patterns used to produce the ceramic molds.
The Best Way to Manufacture Machine Components
Investment cast machine components start just as any other investment casting would: as wax injections using highly detailed aluminum injection dies to produce incredibly smooth surfaces on the patterns and as much detail as needed. For lower volumes or prototype samples, we can 3D print the pattern in plastic and use that in substitution for the usual wax pattern.
The patterns are coated with a ceramic slurry, allowed to dry, and built up layer by layer until a seamless, self-supporting mold is formed. The pattern is melted out, and the mold is filled with a molten alloy suitable for the final application of the component.
We work with our clients and their metallurgical teams to produce castings in highly specialized alloys that perform above and beyond commercially available metals. We manufacture investment castings up to 200 pounds in weight, easily meeting our clients’ requirements for machine component castings.
Applications in Machine Shops for Investment Castings :
Industrial Machinery
Investment casting is used to produce parts like valves, pumps, and fittings that require high durability and accuracy.
Defence and Military
Investment casting is used for components with intricate geometries and high-performance requirements.
Medical Devices
Investment casting is used for parts that require high precision and accuracy, as well as biocompatibility.
Specialized Applications
Investment casting is also used for parts with complex geometries and internal features, such as enclosed impellers, turbine blades, and valve internal parts.
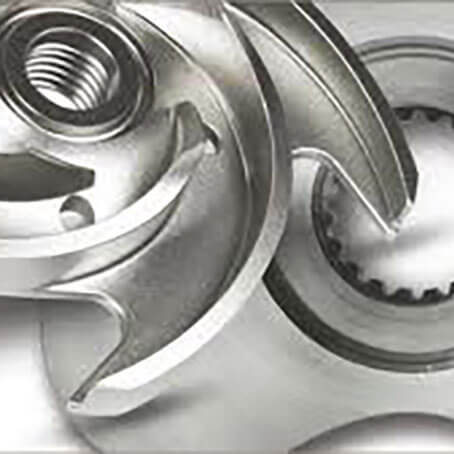
What Machined Components Can Be Investment Cast
The investment casting process offers an unlimited number of possibilities when designing machinery components. Essentially, any metal component can be produced as an investment casting, often offering multiple advantages over other manufacturing processes, such as forged parts, welded assemblies, and sand castings.
Examples of Machine Products Produced by Niagara Investment Castings
- Conveyor parts
- Gearboxes
- Metalworking machines
- Food and beverage components
- Hand and power tools
- Agricultural tractors and implements
- Wire product production machinery and parts
- Railway parts
- Medical devices
- Truck and bus components
- Marine and boat components
- Stoker components
- Water purification and filtration components
- Aircraft parts and airport machinery
- Hardware
- Meters
- Bushings and bearings
- Chain link components
Advantages of Investment Casting for Machine Builders
There are many reasons why manufacturers choose investment castings to machine into the types of components used in today’s machinery. Investment casting offers machine shops a way to produce complex, near-net-shape parts, reduce machining time and overall costs.
The investment casting process is particularly beneficial for parts with intricate geometries, internal features, and tight tolerances. By casting components to a “near net shape” and including difficult-to-machine features, machine shops can minimize material removal and subsequent finishing operations.
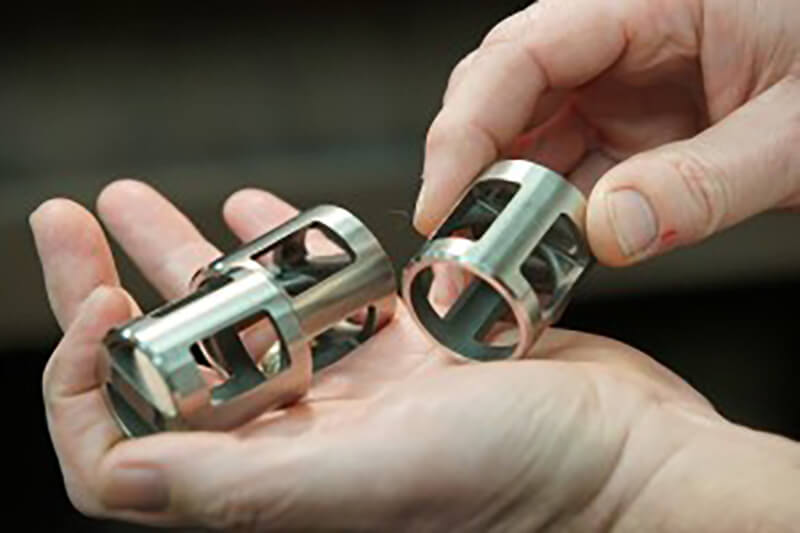
Choose Niagara Investment Castings for your Machining Investment Casting Applications
We can work with you to convert any machined, welded fabrication, forging, assembly, or sand casting to an investment casting to provide you with the many benefits the process offers for any metal component you need to build your machines.
For prototyping of ideas for conversions, or simply for low-volume casting projects, our 3D printed plastic patterns eliminate the need for tooling and offer you a fast way to get your ideas into actual metal components.
Contact us here to start the discussion today.