In manufacturing, stainless steel investment casting is a testament to the blend of art and science, precision and craftsmanship. This process involves creating a wax model, building a ceramic shell around it, and then pouring in molten stainless steel, which is meticulous and detailed. It requires not only technical knowledge but also a deep understanding of the unique properties of stainless steel. This article delves into the key design considerations that can make or break the success of stainless steel investment castings, providing insights into the process, the benefits, and the challenges involved.
Understanding Stainless Steel Investment Castings
Stainless steel investment castings are a cornerstone of many industries, providing strength, corrosion resistance, and excellent surface finishes. The unique properties of stainless steel make it an ideal material for investment castings, with various stainless steel alloys and grades offering a range of mechanical properties to suit different applications.
Investment Casting Process
The investment casting process is meticulous, beginning with creating a wax pattern that replicates the final product. This pattern is then coated with a ceramic shell, layer by layer, to form a mold. Once the shell is complete, it is heated to remove the wax and harden the ceramic, creating a perfect mold for the molten stainless steel. X-ray equipment is used throughout this process to ensure the integrity of the stainless steel precision casting part.
Designing for Optimal Results
When designing stainless steel investment castings, several key considerations must be remembered. The casting size should ideally be within the ounces to 50-pound range and fit into a 16″ cube with gating for the most economical results. Abrupt changes in cross-section should be avoided whenever possible, as symmetrical shapes with uniform walls and cross-sections cast with less distortion.
The stainless steel casting material should be designed to be gated in one location, preferably in a machined area. This yields more parts per mold but also aids in the dimensional stability of the casting and reduces the areas of the component that will show a gate contact area.
Considerations for Larger Castings
While larger and heavier castings are possible, they often come with challenges. The typical accuracy of an investment stainless steel casting process can be compromised due to the tolerances associated with larger sizes. Additionally, the costs can be significantly higher than alternative processes when investing in large parts.
Benefits of Stainless Steel Investment Casting Components
Investment cast stainless steel components offer several advantages. They provide high levels of detail, consistent and repetitive close tolerances, and can be used to produce intricate internal passages. No other casting process for high melting point alloys like stainless steel comes close.
Tolerances and Surface Finishes
Investment cast stainless steel components typically have tolerances of +/-0.010″ for the first inch of any linear dimension, then another +/-0.005″ per inch of additional linear size. The as-cast surface typically has a finish of 125 RMS, providing a balance between smoothness and the ability for the surface to hold a finish.
Combining Multiple Parts into a Single Casting
One of the key advantages of investment casting is the ability to combine multiple parts typically used for assemblies or weldments into a single casting. This simplifies the manufacturing process and can lead to significant cost savings.
Machining and Draft Considerations
Investment castings that require machining to finish any dimensions tighter than cast tolerances can be designed with much less material for finishing due to the stability and repeatability of the stainless steel casting. Unlike sand casting processes, no draft is required to produce investment castings, resulting in significantly more accurate dimensions of the stainless steel casting.
Volume Considerations and the Use of 3D-Printed Plastic Patterns
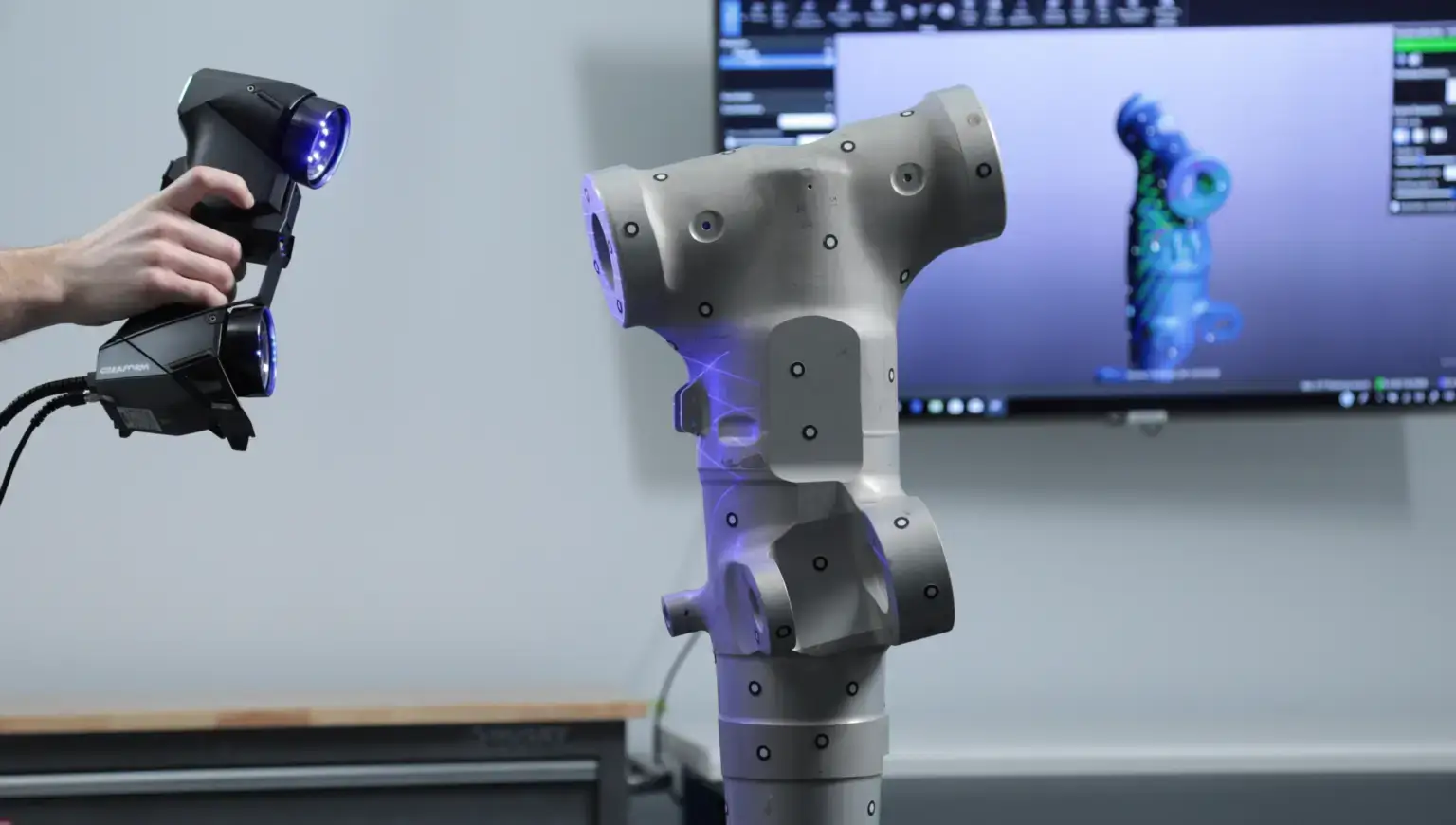
For low volumes, the one-time cost of wax injection tooling may be prohibitive to use investment castings. However, for larger volumes (100 or more) and designs at low risk of changing, the cost of the injection tooling is generally a very low startup cost considering the cost savings in machining, reduced weight, etc. For low volumes and test runs, 3D-printed plastic patterns can be substituted for wax patterns, allowing the investment cast part to be still produced.
Time Considerations in Investment Casting
The overall time to produce an investment casting is generally 4 to 6 weeks due to the time needed to form the ceramic shell, which is a layer-by-layer application process. Investment casting is one of the longer casting processes, and the long lead times should be considered.
Wall Thickness and Flatness Considerations
Wall thicknesses in the thinnest part of the casting should be at least 3/16″, possibly heavier depending on several factors. The flatness and straightness of an investment casting can be difficult to maintain and should be considered when designing the casting. Mechanical straightening of the casting or a machining operation of the surface should be expected if flatness or straightness is paramount.
Limitations and Recommendations
Threads, gear teeth, and splines cannot be cast in due to runout issues between mating surfaces. Part numbers and logos should be cast using raised lettering inside a receded pad for best results.
The Role of Stainless Steel in Various Applications
Stainless steel plays a crucial role in a wide range of applications. From turbine blades and surgical tools to food processing machinery and coffee machine components, the versatility and durability of stainless steel castings make it an ideal material for investment castings. It’s also widely used in pump and valve applications, where its corrosion resistance and strength are highly valued.
Frequently Asked Questions
What types of stainless steel are commonly used in investment casting?
Various types of stainless steel are used in investment casting, including austenitic stainless steel, duplex stainless steel, and martensitic stainless steel. The choice depends on the specific requirements of the casting, such as corrosion resistance, heat treatment hardness, and mechanical properties.
Can investment casting be used for creating parts with internal passages?
Yes, one of the advantages of investment casting, especially when using stainless steel, is the ability to produce intricate internal passages. This makes it a suitable method for creating complex shaped components that would be difficult to achieve with other casting methods.
How does the surface finish of investment cast stainless steel components compare to other casting methods?
The surface finish of investment cast stainless steel components is typically 125 RMS, which is smoother than many other casting methods. This and the process’s ability to produce parts with excellent dimensional precision make investment casting a popular choice for applications where surface finish is critical.
The Path to Successful Stainless Steel Investment Castings
Design considerations play a crucial role in the success of stainless steel investment castings. From the initial design phase to the final product, every decision can impact the quality, cost, and performance of the casting. By keeping these considerations in mind, you can ensure that your investment castings meet the highest standards of quality and performance.
If you’re ready to explore the possibilities of stainless steel investment casting for your next project, contact the experts at Niagara Investment Castings today. We’re here to guide you through every step of the process, ensuring a final product that meets your exact specifications.