Niagara Investment Castings produces investment castings for a wide range of industries, and the popularity of using the investment casting process to manufacture components is due to many advantages over other processes. One of the biggest advantages is the high-quality surface finish of the casting.
What is The Surface Finish for Investment Castings?
A typical investment castings surface finish for a high-temperature alloy such as steel, stainless steel, tool steel, or other high-melt point alloys is expected to be around RMS120.
This is significantly smoother than the minimum RMS560 of a typical sand molded casting, which is generally considered the predominant alternate casting method for these high melt point alloys.
This allows for significantly tighter tolerances being able to be held, typically following a rule of +/-0.005” of tolerance per linear inch of any dimension.
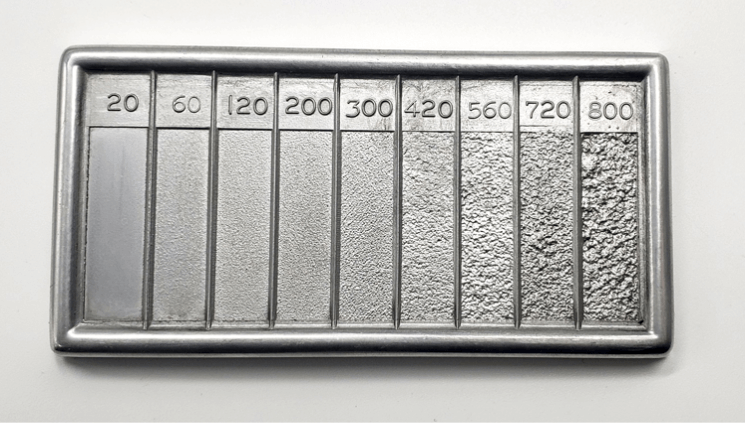
Not only is the surface finish of an investment casting superior to that of sand castings but no draft is required to be added to any vertical walls of the casting, again increasing the ability to cast to much higher tolerances.
Why Does Investment Casting Create a Better Surface Finish?
The key difference between investment casting and other casting techniques can be attributed to the quality of the wax pattern, and the characteristics of the seamless ceramic mold formed around the pattern.
The wax patterns are formed by injected melted wax into an extremely smooth and highly polished aluminum die. This allows for the wax pattern to possess the same smooth surface as the tooling.
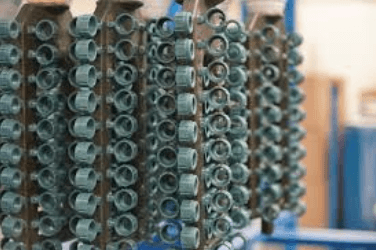
The surface finish of the investment casting is due to the ability to transfer the smooth surface of the wax to the casting. This is done by first utilizing a fine primary coat of high-grade refractory material in a liquid “slurry” form.
The wax pattern is dipped, or “invested,” into the slurry, and a fine layer is retained on the wax. Eventually, this layer will dry into a solid form of ceramic. Multiple dips are then added one at a time to secure the strength of each prior layer of ceramic.
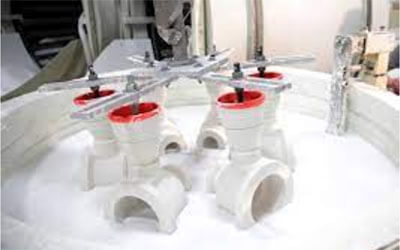
This creates the basis of a ceramic shell around the wax pattern with a very smooth interior wall. It’s the smooth surface of the interior of this shell that is directly responsible for the fine surface finish of the castings that it will eventually produce.
Investment Casting versus Die Casting
There is typically only one other casting process which would provide BETTER than the RMS120 finish attainable with investment casting, and that is casting techniques where the metal itself is allowed to solidify against a highly polished solid mold surface, such as a steel die used when die casting.
However, due to the high temperatures involved when casting most metals OTHER than aluminum, zinc, lead, or similar low melt point alloys, metal molds are not able to be used as they would be damaged or destroyed by the high temperatures. This means that investment casting is the ONLY casting technique that can be employed for high melting point alloys when a superior surface finish is required.
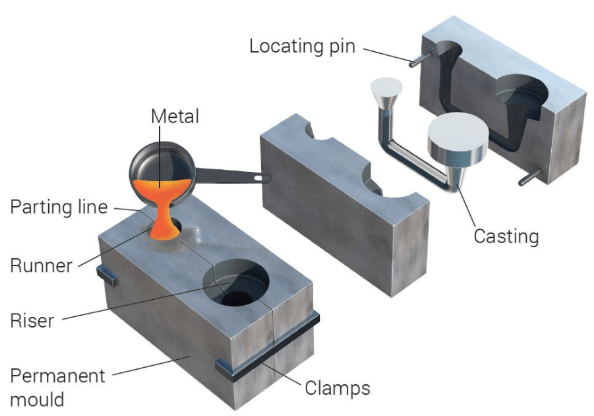
Advantages Related to the Superior Investment Casting Surface Finish
There are many advantages that designers should take into account when considering the benefits of a superior surface quality when specifying investment castings. These include as a minimum :
Dimensional Accuracy
The high quality and smooth surface finish that can be achieved provides a major advantage in terms of dimensional accuracy. Investment castings can be produced with higher dimensional accuracy than castings manufactured using other processes, making it a more appropriate production method for components that need to be produced with higher levels of precision.
Reduced Machine Stock Required
The cost of machining can often be reduced by using investment castings versus sand molded castings. While investment castings may appear more expensive than other castings, the higher grade of surface finish can remove the need for excessive machining to achieve the required finish.
This can result in cost savings when comparing the prices of producing fully finished components from sand castings, forgings, and welded assemblies.
Design Challenges Can be Eliminated
When challenging features are required in a component, carrying out machining operations to form these features can be impractical. When the design of a component involves complex shapes and complex internal features, investment casting not only is a key method to produce the design, but also ensures that parts can be manufactured to the necessary specifications without compromising design intent when machining is altogether impractical or not permitted.
Additional Surface Enhancements
When even higher levels of surface finish are required for non-machined surfaces, investment castings can easily be polished, electropolished, or vibra-finished in a multitude of various media, to produce the desired finish, including a mirror finish. The high level of surface smoothness of the investment casting allows for ease of achieving these higher levels of finish when needed fast.
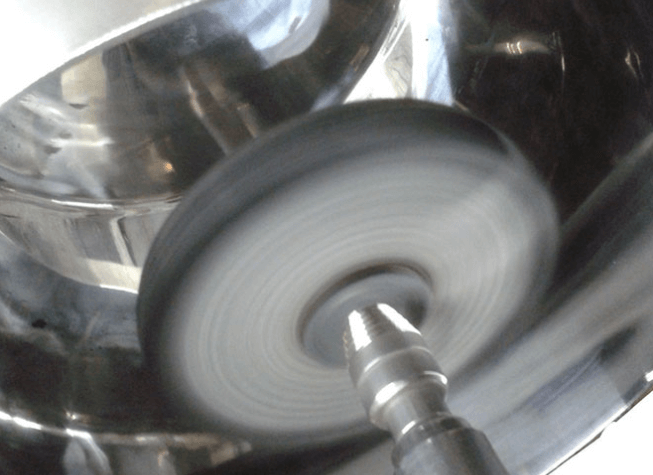
Choose Niagara Investment Castings for Your Investment Cast Applications
With decades of experience manufacturing high quality investment castings, we are proud of our history of utilizing this unique manufacturing process to satisfy our clients requirements across a broad range of industries.
Our dedicated and experienced team at Niagara Investment Castings are here to help for any support in how the superior surface finish of investment castings may just be the perfect solution for your component manufacturing.
Please simply contact us here to start the discussion!