Niagara Investment Castings manufactures investment castings utilizing a wide array of the most up to date technology available.
One of the most important tools we have is solidification modelling. We use it in the early stages of product design. This ensures that the castings we manufacture are as sound and free from solidification shrinkage defects as possible, within the limits of design and cost.
What is Solidification Modelling?
In its simplest form, solidification modelling is the process of using computerized “real time” simulation of the entire casting process, including the mounting of pattern waxes on a specific sprue, the casting or filling, the solidification, and final cooling to room temperature, generally applied to new castings.
The software used for solidification modelling takes into account many variables, including alloy composition, pouring temperatures, gating size and contact points, among many other crucial datapoints.
This software takes many theories into account, including fluid flow equations, complex algorithms, and heat transfer formulas, and the level of complexity of the software is well beyond the scope of this article.
Only a handful of companies produce and distribute this kind of software for the investment casting industry, and users generally need a high level of training to utilize the software to its maximum advantage.
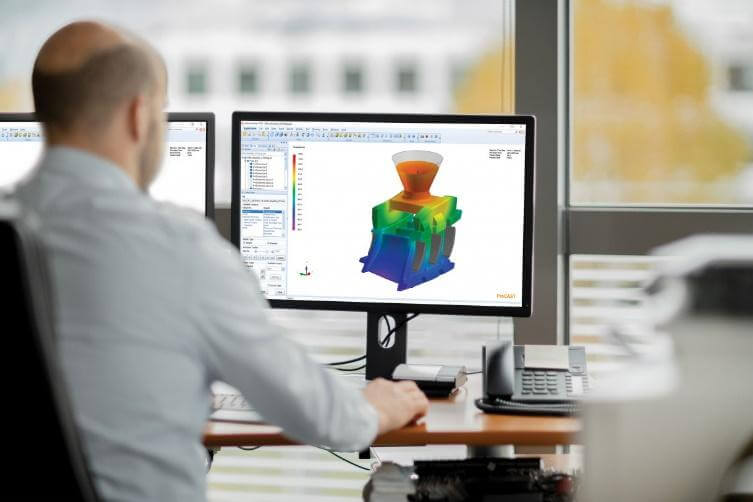
The Solidification Modelling Process
The solidification modelling process is a 3D technology intended to graphically demonstrate where the software “predicts” shrinkage-type defects that may occur in the final cast component.
- Our engineers generate designs for gating and use the software to validate the designs. The process for the first article sampling then begins.
- First, our engineering team will run a “casting only” or “bare” solidification which will identify the areas of risk in the part. This will assist in the design of the gating, the metal delivery system, and any other critical design features of the feeding system.
- After the gating rigging is designed, the team then simulates the filling of the part. The software will predict areas where we could see potential defects caused by the metal filling. It also shows the metal solidifying and cooling.
- Our engineers will then adjust the gating and rigging design to reduce the risk of potential defects and run multiple iterations of the design changes until the issues are resolved.
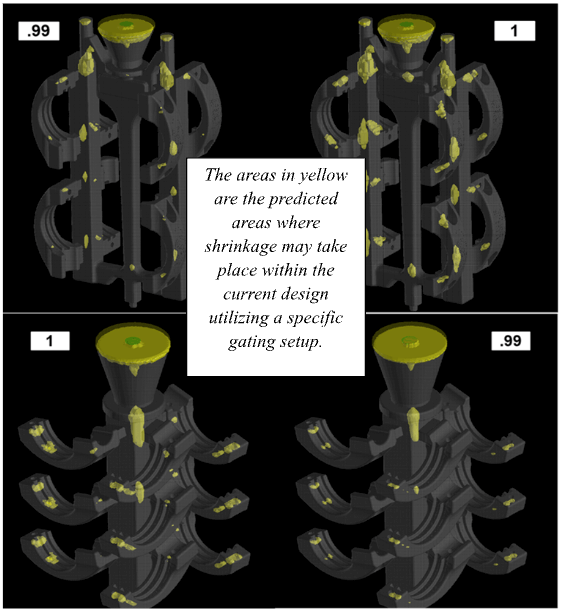
Applying Solidification Modelling to Investment Casting
One of the greatest technological advancements in the foundry industry in recent history is the use of solidification modelling to engineer the design of the castings and how they will be gated.
Foundries are essentially businesses that cast metal into molds. In the investment casting process, metal melted at approximately 2500 degrees F. can then flow into molds produced from ceramic shells.
A significant issue, however, is that as the metal cools and returns to a solid form inside the mold, shrinkage will occur since the volume of the liquid that has entered the mold is greater than the volume of solid metal. So, a constant feed of new molten metal must be available to fill any voids that form from shrinkage.
Investment casting utilizes a unique combination of feed sprues and “gates,” which serve a dual purpose. The first is providing a rigid point, or points, of support of the pattern to the feed sprue and the point at which the molten metal will not only enter the cavity of the ceramic mold but, more importantly, to provide this “feeding” of the molten metal into the cavity to backfill new molten metal into voids formed as the metal solidifies.
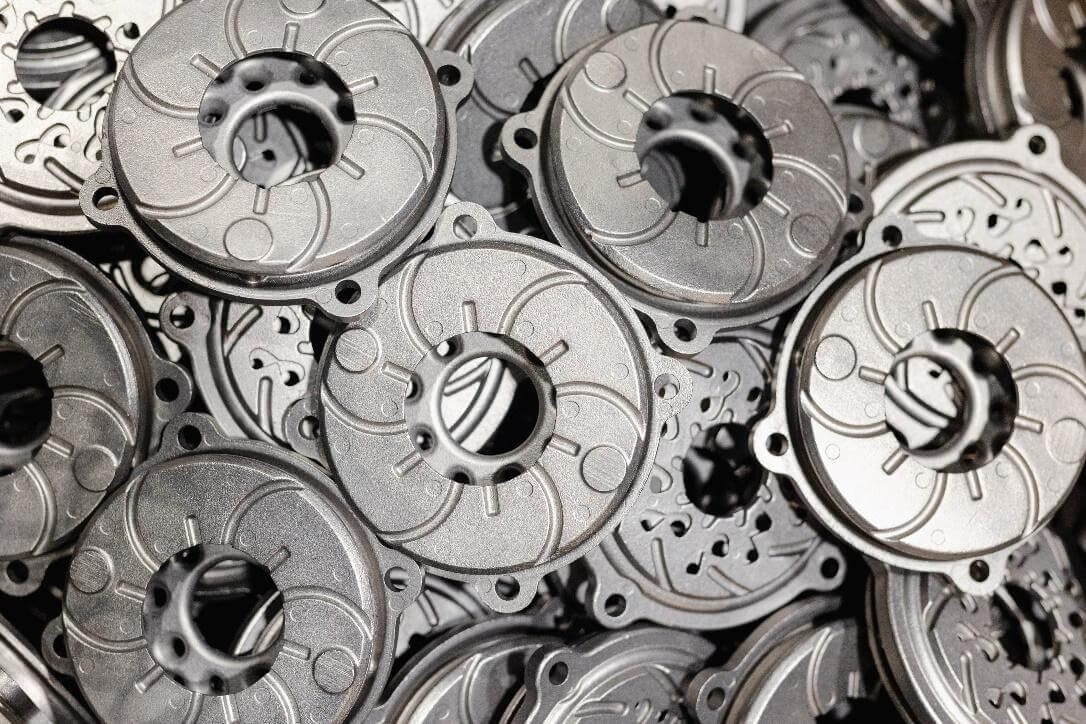
Finished castings with round “gate witness” of where gates were determined to be most effective using modelling.
Advantages of Solidification Modelling
There are many advantages of utilizing solidification modelling when working with our customers to develop not only the ideal casting geometry for the components they wish to cast, but also allow Niagara Investment Castings to be able to “cast” the component in a real-time simulation, saving time, cost, and materials.
Specific advantages include the following :
- The process is applicable for almost any of the cast alloys we offer. It considers all aspects of casting manufacture, including melting and metallurgy, tooling, and cutoff/finishing.
- Provides a virtual “real world” test of a gating design with the goal of reduction/elimination of metal casting defects with high degrees of confidence.
- Establishes optimized operating points for quality, yield and cost.
- Identifies optimal process conditions for robust process windows early and reliably
- Allows faster decision-making to establish saving time for all parties involved
- Empowers both NIC and our customers by generating a systematic understanding of how process variability affects quality, and improves communication and confidence within our company and in cooperation with customers
- Offers reliable and early information to designers for robust product and process development
Choose Niagara Investment Castings for Your Investment Cast Applications
With decades of experience manufacturing high-quality investment castings, we are proud of our history of utilizing this unique manufacturing process to satisfy our clients’ requirements across a broad range of industries.
Our dedicated and experienced team at Niagara Investment Castings is here to help with cutting-edge technologies such as solidification modelling.
Please simply contact us here to start the discussion!