As the name implies, Niagara Investment Castings produces a type of casting that is known around the world as “Investment Castings”.
While this process is also known to a lesser extent as both “Precision Casting” and “Lost Wax Casting”, there is much confusion about the term “Investment” when it comes to understanding the process.
Our expertise and experience in casting the many types of components we offer are helpful when our clients want to take advantage of the unique benefits of investment casting. However, we often find that our potential new clients are concerned that the process is named investment casting due to the perceived high cost of the process. Nothing could be further from the truth. Let us explain.
What is Investment Casting?
The liquid ceramic slurry that will eventually form the mold can encapsulate the disposable pattern in one of two ways. The more uneconomical method is to pour the slurry around the patterns in a flask container and allow the ceramic to solidify into a solid block of ceramic. The pattern is generally left solid in the mold, and the extreme heat of the molten metal burns it away as the metal is poured into the mold. This method is more costly due to the amount of ceramic used to form the mold, as results in much more work needed to remove the finished casting from the solid block of ceramic. As a result, it is NOT the commonly used method for ceramic mold casting of high alloy metals, however, it is very commonly used when casting small objects, such as casting jewellery from gold.
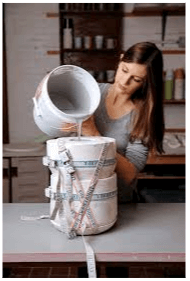
The preferred and most cost-effective method of utilizing ceramics for casting is investment casting. This method uses a dipping technique to apply “layers” of the liquid ceramic slurry together with loose grains of refractory sand. This layer is allowed to dry, and the process is repeated several times to build a suitably strong shell around the patterns. It is this dipping technique that gave this process the name investment casting. The following diagram illustrates the steps involved in the process.
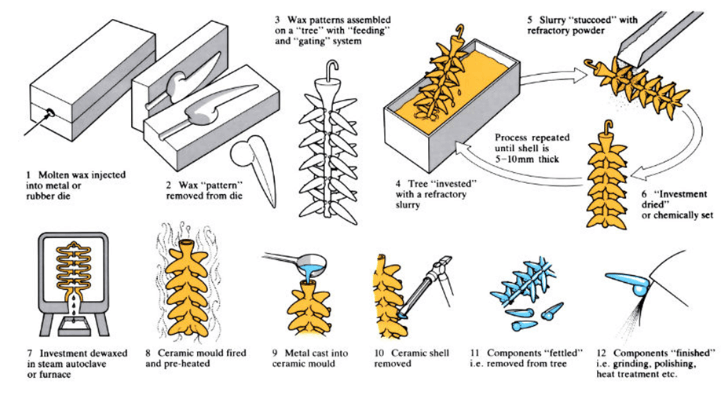
What is Invested in Investment Casting?
Placing an object into a liquid media, and a portion of that liquid remaining on the surface of the object once removed from the media, is the process called “investing”. In the simplest example, placing your arm into a bucket of water, and pulling it out, leaves your arm wet. You have carried out the investing process by some of the liquid sticking to, and remaining on, your skin.
In the investment casting process, the disposable patterns are what is dipped into the tank of ceramic slurry, and on the initial dip, a thin layer of the liquid ceramic remains on the surface of the pattern. It is dusted with fine sand and allowed to dry to a solid ceramic layer. Following this drying, subsequent investing dips are performed, with the ceramic now adhering to the previously applied layer, until a “shell” is formed that is between ¼ to 3/8” thick.
This shell is now ready to have the pattern removed via either steam autoclave or burning it out and firing the green ceramic to form a stronger bond. This fired ceramic is strong enough to withstand the high temperature of the molten metal that will be poured into it.
Ceramic Molding vs. Sand Molding
One inherent characteristic of any mold used for casting metal is that it must be able to withstand the extreme temperatures of the molten metal being poured into it to form the shape of the casting. This is especially true since the mold will be subjected to these levels of heat for an extended period of time as the metal cools and returns to a solid form.
Some metals, especially non-ferrous alloys, melt at low temperatures and can be cast directly into metal molds made of higher melting point materials. An example of this is when aluminum is poured, or injected, into a steel mold to form “die castings”. The steel mold will allow the aluminum to take shape, and cool down to a solid, and then the tool is opened and the finished part removed, and then cycles over and over again in this manner.
Higher melting points alloys, such as steel, stainless steel, nickel alloys, and cobalt-based alloys, are the most commonly used metal alloys in industry, and cannot be poured into metal molds, as they will immediately cause the mold to melt due to temperatures of the molten alloys that are approaching 3,000 degrees Fahrenheit. These alloys must therefore be cast into molds that are made from “refractory materials”. Refractory materials are those which will withstand extremely high temperatures before they break down or melt. In the world of metal casting, these materials are typically either silica sand or ceramics made up of oxides of common minerals. These can include alumina, silica, and zirconia.
Sand molding involves ramming loose sand around a pattern that will leave the impression of the pattern in one half of a mold. The patterns are designed and manufactured so that they can be removed from the sand once the bonding agent of the sand causes the sand mold to harden into shape. These bonding agents can range from clay to a variety of chemicals used to fuse the grains of sand together. Once the pattern is removed, the halves are placed together to form a mold which the molten metal is poured into and allowed to cool.

Ceramic molds, on the other hand, are made from a mold material that starts as a liquid form of a refractory material, generally one or more of the rare earth oxides suspended in a liquid colloidal silica gel. This mix of refractories is called a “slurry”. Since these liquid slurries will “flow” around a pattern and turn to a solid once dried, the pattern itself cannot be removed from the finished mold in one or more solid pieces to be re-used over and over again, and therefore ceramic molding must use disposable patterns. These patterns are made from expanded foam, wax or plastic so that they can be melted or burned out of the finished mold.
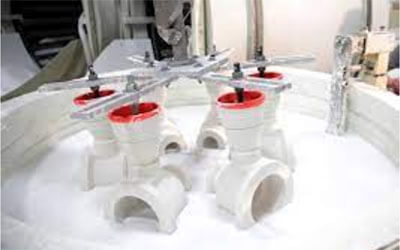
Other Names for The Investment Casting Process
Remember that one of the key characteristics of the two ceramic molding processes is that the disposable patterns must be melted or burned out of the ceramic mold to expose the cavity which will be filled with the molten metal. This “loss” of the wax pattern is unique to the investment casting process, and the “lost wax process” is, therefore, one of the names often used to describe an investment casting.
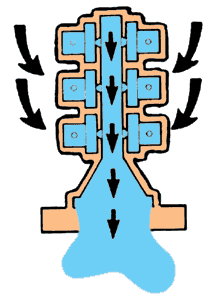
A second commonly used term to describe the investment casting process is “precision casting”. This comes from the higher tolerances attainable with investment casting, versus the other commonly used casting method for high temperature alloys, which is the sand molding process.
Choose Niagara Investment Castings for Your Investment Casting Applications
With decades of experience manufacturing high-quality investment castings, we are proud of our history of utilizing this unique manufacturing process to satisfy our client’s requirements across a broad range of industries. Our dedicated and experienced team at Niagara Investment Castings are here to help with any support in how investment castings may just be the perfect solution for your component manufacturing. Please simply contact us here to start the discussion!