Niagara Investment Castings has the expertise to work closely with our clients to help them understand and overcome potential problems related to one of the most misunderstood characteristics of the casting process ….. shrinkage.
Our expertise and experience in casting and tooling design can assist our clients when it comes to applying the rules of casting shrinkage and how to deal with the many concerns that this phenomenon can cause if not addressed properly.
If you require assistance with any concerns related to casting shrinkage for your specific application, please just ask your Niagara Investment Castings Sales Representative, and we will be happy to assist you with casting shrinkage and how to avoid potential problems.
What Does “Shrinkage” Mean in Terms of the Investment Casting Process
Shrinkage is an internal change in volume that occurs in the casting mold during a phase change in a metal’s transition from a liquid state to a solid state. This phenomenon occurs in every type of metal casting process.
Metals undergo contraction when solidifying and cooling, because the specific volume is larger in the liquid state than in the solid state for standard casting metals. Therefore, it is a function of the casting material.
In metals, shrinkage occurs in three phases:
- Liquid Shrinkage
The liquid solidification phase is simply the change in volume of the metal as it cools while still in the liquid form, similar to the “solid” phase, whereas materials are larger at higher temperatures than they are at lower temperatures, and contract as they cool. This phase is of little concern in the investment casting process as the metal will easily fill all spaces once cast into the mold and continue to occupy available space while in the liquid form. - Solidification Shrinkage
The solidification shrinkage phase is a phenomenon that is of greatest concern in casting, as it leads to voids and cavities when there is not enough molten metal to feed the shrinkage when casting. Areas of the casting with the greatest cross-section are the last to solidify, so the probability of shrinkage is increased as the size of the section increases. Closely related to this is that areas that are hotter for a long time, such as these heavier sections OR any part of the casting that stays hot due to placement on the sprue, will solidify later than the surrounding sections. - Solid Shrinkage
The solid shrinkage phase is similar to the liquid solidification phase, only now in a solid form. Once again, the metal will continue to shrink down in size as it cools from the high temperature of casting, down to room temperature.
The various forms of shrinkage results in several casting defects such as incorrect linear dimensions, open voids on the surface of the casting, or hidden porosity in the product.
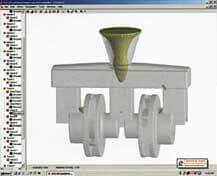
How to Calculate Shrinkage Allowance in Casting
Depending on the alloy, the allowance for solid shrinkage allowance in casting is usually a specific percentage that is applied to all dimensions when building the wax injection tooling. These dimensions in the tooling are cut LARGER than the target dimension by this amount.
For instance, the shrink rate for stainless steel is generally around 2.8%. For other alloys, it can be considerably different. For example ductile iron can vary from as little as zero on up to 1%.
Another contributor to variation is part geometry (section thickness & shape, the presence of ribs, bosses, etc) and the use of cores in the mold. Generally speaking, a complex geometry will have a less predictable shrink rate. This must be taken into account when applying shrinkage in tool design and is an area where the skill and experience of the toolmaker is most important.
The use of the proper shrinkage allowance in the design of your investment castings is crucial. Our team of experts know exactly how to apply the correct shrinkage rate of the alloy for your specific application. Start by visiting our REQUEST A QUOTE page let us know how we can be of service.
How to Avoid Shrinkage in Casting
The contraction of the metal during both liquid and solid is dealt with by adding the shrinkage allowance discussed above to the tooling. However, the solidification shrinkage is a completely different issue that requires a unique approach to prevent this volumetric reduction in size from causing shrinkage “voids” or porosity in the casting.
These shrinkage related defects in investment cast products can lead to failure, leakage, unacceptable visual flaws on the surface, and other concerns. Sometimes these defects appear on the surface of the casting and can be detected visually or through dye penetrant or similar non-destructive procedures. Sometimes the defects are internal to the casting and require X-ray inspection or destructive tests to uncover. These defects are collectively known as open- and closed-shrinkage defects.
Open Shrinkage Defects
If the metal cools and shrinks with insufficient liquid available to fill any voids, pipes may form in the surface and extend into the body of the casting. Similarly, defects that form on the surface and spread across the face are sometimes called cave defects, or sinks. In both instances, the defects are open to atmosphere and air takes the place of molten metal.
Cracks and hot tears usually form in the final stages of solidification and can be localized around abrupt changes where stress concentration exists such as a thin web connecting two heavy sections. They can also occur in heavy sections where heat pools.
Closed Shrinkage Defects
Porosity is one of the most common defects in castings, as without fully effective “feeding” of the casting, it will be inherent in every cast product produced. However, not all closed shrinkage is considered a defect, as in many cases it cannot be avoided due to geometry, and often does not weaken the casting in any way.
Open shrinkage porosity is by far the most common type seen due to the ability to quickly detect it on the surface of a cast part by what appear to be small holes or cracks. Thick parts with varying cross-sections throughout are most susceptible to such shrinkage, which occurs as the metal cools and solidifies in a non-uniform pattern.
Porosity can exist in the interior of a casting as well, without necessarily showing on the surface of a part. This occurs when liquid metal is surrounded by solidified metal and molten metal is unable to fill in behind the liquid as it cools and shrinks. This is called “Closed Shrinkage”.
As mentioned, the most common causes of shrinkage are related to the casting sprue and ingate location and size, which is the passage through which molten metal is poured into the investment casting mold. Differing cross-sections require different considerations. For instance, in areas such as the heavy sections of the casting, the metal takes longer to contract and solidify, which reduces feed material availability and increases the likelihood of shrinkage, especially if the ingate is too small for the volume of flow. A properly sized ingate and correspondingly properly sized sprue attached directly to the heavy section can fill the shrinkage cavity and provide the feed material necessary to counteract shrinkage as cooling takes place.
Casting Simulation Software
Specially designed software is used at Niagara Investment Castings to optimize the filling of cavities through ideal gate designs and can predict the occurrence of shrinkage porosity. The flow and feed of material through the mold can be controlled by good gating design and placement, as well as employment of techniques such as directional solidification.
This technology is applied to every new job we take on. In fact, we will cut the optimum gating into the tooling, or print it as part of the pattern when utilizing 3D printed plastic patterns for our prototyping service, once this software has been used to design the optimum gating and tested in sampling.
Other shrinkage defects aside from typically larger voids in the casting can include:
- Sponge shrinkage usually arises in the thicker mid-section of the casting product and causes a thin lattice texture similar to filament or dendrites to develop.
- Filamentary shrinkage results in a network of continuous cracks of various dimensions and densities, usually under a thick section of the material. It can be difficult to detect, and the fracture lines tend to be interconnected.
- Dendritic shrinkage fractures are narrow, randomly distributed lines or cavities that are often unconnected. They are typically thinner and less dense than filamentary cracks.
Casting Shrinkage Compensation
Metal shrinks as it transforms from liquid to solid (known as solidification shrinkage) and undergoes additional thermal contraction as it cools to room temperature. Cast parts are therefore designed with shrinkage allowances to result in parts of the desired dimensions. Cast steel, for example, will shrink about ¼ in. per foot. Shrinkage allowances are known for various metals and an experienced tooling designer will take the shrinkage into account when designing a mold. For more information on casting designs in general please refer to our information page here.
Pattern shrink, not to be confused with the casting defect shrinkage porosity, is an allowance made on patterns, molds, and cores to compensate for the dimensional changes as a casting cools. Today, “shrink” is more commonly applied as a scale factor to the 3d CAD file during tool build.
Conclusion and Summary
Because of the variables involved, dealing with the various forms of casting shrinkage is essentially an educated “best guess” of how the casting will contract after solidification and should not be considered universal across the industry, although most foundries generally use a similar shrink for a given alloy.
Since it is linear, as a casting gets larger the total amount of casting shrinkage a part will experience as it cools is greater, which magnifies the effect of pattern shrink error. This is why the tolerances for an investment casting get more liberal as the dimension in question gets larger. Typical investment casting tolerances for castings produced from tooling is approximately plus or minus 0.005” for every inch of any dimension.
As for solidification shrinkage, Niagara Investment Castings utilizes industry leading software to minimize porosity type defects caused by ineffective gating whenever possible. However it should be kept in mind that 100% removal of ANY internal shrinkage is often impossible to achieve, considering that multiple cross sections can exist in a casting, rendering inaccessible areas for gating. Castings that require zero casting shrinkage porosity are often checked using radiography and are often subject to intensive design modifications as part of our review of the most optimum gating scenario. We are here to answer any questions or concerns about your casting designs, please just contact us here to start the discussion!!